Mosaic is handcrafted and Damascus, Syria art of wood and shells
Mosaic is handcrafted and Damascus, Syria art of wood and shells.
Despite the decline in its production in Damascus and Syria due to the war, it was able to establish a presence in other countries such as Turkey and Jordan, moving with its craftsmen, most of whom are Damascene, who are the original people of the “mosaic” craft.
In this report, we try to shed light on the reality of the Damascene “mosaic” craft inside Syria, the changes it has undergone, and the difficulties it faces, while tracing its craftsmen and successes outside the borders.
In Damascus and its countryside, Mustafa (42 years old) moves to his workshop dedicated to making Damascene “mosaic”, a craft he has been practicing for more than 30 years.
“Certainly, the craft does not die, and it will not die,” said Mustafa (a pseudonym for security reasons), who began working in the “mosaic” craft since the age of ten, describing to Enab Baladi his passion for making ornate wooden boxes decorated with seashells, for which the Jobar neighborhood was famous. Damascene from which he hails.
“My workshop is in the Levant, and I work within the Levant, and for this craft, mosaic, the last ten years have certainly affected many fields, but especially these handicrafts, the demand for them has become weak, and the current generation has no desire to learn it,” Mustafa added.
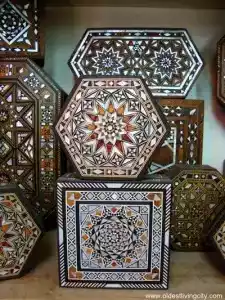
In the Jobar neighborhood since the fifties
The Jobar neighborhood was the largest area with workshops and shops selling “mosaic” in Damascus, according to what Mustafa told Enab Baladi.
“He was the source of interest,” he said, proud that his family’s shops that traded this craft had been in the area, in addition to other shops since the 1950s.
However, the conditions of war and displacement have changed this situation, as the Jobar neighborhood has been subjected to violent battles between the opposition factions and the Syrian regime forces, over the past years, which led to widespread destruction of its buildings.
After that, the workshops and exhibitions moved to the city of Jaramana, which was also famous for the turnout of craftsmen to learn the “mosaic” industry at the hands of ancient Damascene teachers.
Mustafa moved his workshop to Jaramana, and the showrooms to Bab Sharqi neighborhood and Medhat Pasha market.
“Mosaic” is considered a special art in Damascus, and it was Jerji al-Bitar or the one who invented this industry, according to what was mentioned in the history books of the city of Damascus.
Al-Bitar made the first “mosaic” piece in 1860, by collecting rods of naturally colored wood with a triangular or square cross-section, then cutting them in the form of chips and pasting them on wooden crafts with natural glue.
The craftsman Mustafa pointed out the importance of this profession, as it is a heritage confined to Damascus only, as it is not circulated much in other countries. However, during the war period, some craftsmen were forced to transfer their workshops to Turkey, relying on the sale of goods through an external market.
Since the beginning of the 17th century, when nicknames began to be adopted in the Levant, families’ nicknames became indicative of the professions and crafts they inherited and excelled in, as it was a source of abundant livelihood for them.
Including the “mosaic” craft, which was not yet one of the traditional professions and crafts, but was invented by Jerji Gabriel Al-Bitar, who excelled in the Damascene “mosaic” craft, which is now producing the most beautiful antiques that tourists come to Damascus.
From the blog of researcher and historian Joseph Zaitoun, entitled: Jerji Gabriel Al-Bitar Al-Dimashqi, the creator of “mosaic” art
Local wood and imported shells
The manufacture of “mosaic” pieces depends on colored wood that is later fed with shells, whether natural or artificial. Creativity in this craft plays an important role, as it takes a geometrical character in its forms, according to Mustafa, during his talk about the details of the work, “Mosaic is a very wide field, and from It is natural that with practice it becomes like any ordinary craft, but the love of work and creativity in it remains the main factor,” as he put it.
Several types of wood are used in the manufacture of the “mosaic” piece, which is a municipal wood that is available in Syria and does not need to be imported, such as walnut, lemon, olive and eucalyptus, according to Mustafa.
He referred to the diversity of colors, saying, “The black color in the pieces is walnut, the red is close to eucalyptus, the burgundy is the color of roses, and the white color interspersed with it is the color of shellfish.”
He continued, “These pieces are made with geometric shapes and with high accuracy that only the son of the interest can master. Our craft differs from other professions in that it is characterized by smoothness and polishing, as the devices play an essential role in the manufacturing process.”
Mustafa noted that each piece has its own path in work and its unique art, according to the drawings in it.
Each hundred pieces of a medium-sized wood box, for example, which Mustafa called “Khaskar” (every hundred pieces) takes 15 to 20 days to be ready for display and sale, if labor is available.
Regarding the imported raw materials, Mustafa pointed out that the coincidence that enters into the final stages of wood grafting comes from abroad, and it has become difficult to import it because of its monopoly by traders and its high prices.
He added, “Import prices were acceptable in the past, but now they are expensive (high), due to the economic conditions,” and he continued that “among the basic raw materials are types of plastic such as granules, and a type of shell called (Rahaj seashell).”
Among the main machines on which the manufacture of “mosaic” depends, is the “shellah”, a machine on which wood is cut to reach the required geometric shapes.
And also “delicate” and is used to soften the final product, in addition to the “rabob” machine to harmonize wood.
These machines were previously available to everyone for people wishing to practice the craft, but there have become difficulties in securing them due to their high prices, in addition to the machines’ dependence on electricity, the interruption of which has become a burden on craftsmen and their having to resort to electric generators, which disrupts the speed of production and increases costs, according to what Enab monitored. My cross-country of interviews with “mosaic” craftsmen.